5月16日,东方电气自主研制的国内首台单机容量最大功率150兆瓦级大型冲击式转轮成功下线,实现我国高水头大容量冲击式水电机组关键核心技术国产化“从无到有”的历史性突破,开启了我国水力发电产业高质量发展的崭新篇章。
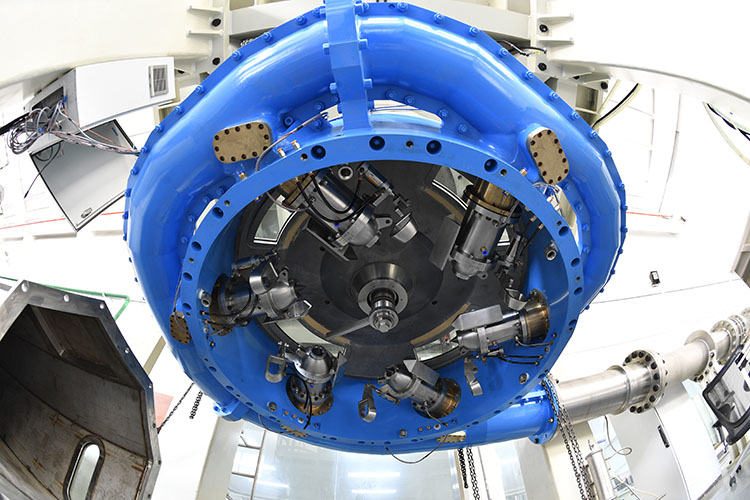
本次下线的冲击式转轮重约20吨,最大直径约4米,将用于四川省雅安市田湾河流域金窝水电站,预计6月初投入运行,届时将为国内单机容量最大的冲击式水电机组装上“中国心”。
依托150兆瓦级大型冲击式转轮国产化项目,东方电气冲击式转轮水力开发、造型设计、软件开发、模型装置研制等实现了完全自主化,填补了多项国内技术空白;转轮结构设计、材料应用、加工工艺等关键核心制造技术取得了突破性进展。
牢牢把关键核心技术掌握在自己手中
在水力开发方面,转轮研发创新应用了东方电气自主开发的具有完全知识产权的冲击式转轮三维造型软件,解决了自主化设计的建模难题;应用了先进的仿真分析计算方法,提高了转轮水力开发、设计优化效率。
在结构设计方面,设计团队验证分析了一百多个方案,优化了转轮三维高阶复杂曲面造型,优化应力分布,确保转轮循环疲劳寿命不低于15亿次,综合考虑振形与激振频率、转轮固有频率在不同介质中的差异,执行1到17阶频率校验检查,转轮水斗每秒承受高速水流冲击范围37.5次至637.5次,解决了大型冲击式转轮结构设计方面的难题,确保转轮性能优异,结构安全可靠。
在工艺制造方面,转轮中心体采用锻件与复合增材结构,降低了锻坯制造难度,提高了材料利用率。转轮应用高精度数控加工工艺,实现转轮水斗异形深腔高效铣削、水斗型面高精度铣削。转轮外部水斗采用3种制造方式,有效验证了不同制造方式的适用性,为更高水头更大容量冲击式转轮研制积累了宝贵经验。
40天完成2700千克金属增材
150兆瓦级大型冲击式转轮生产制造创新应用了机器人电弧增材制造技术(3D打印),3台机器人历时40余天协同作业,完成2700千克金属增材,开创了行业先例,突破了转轮锻件制造难题,降低锻件厚度,进一步降低锻坯制造难度,有效减少后期机械加工量。
机器人电弧增材制造充分融入数字化技术,高度适用于冲击式转轮外部水斗复杂型面结构部件的制造,实现了远程操控与多机器人无人值守作业,实现定制化设计和制造的“近净成形”(所焊即所得)。
开启我国水力发电产业高质量发展新篇章
研制高水头大容量冲击式水电机组是适应我国西部水电基地高原峡谷建设环境条件,实现平衡发展和环境保护的最优方案。
受应用市场缺乏、研发投入不足等因素影响,我国发电装备企业在高水头大容量冲击式水电机组的自主研发、设计、制造和运行等方面基础较为薄弱,与国外先进企业存在差距。
2019年开始,东方电气全力组织开展高水头大容量冲击式水电机组关键技术研究。2020年,东方电气成功建设具有世界先进水平的冲击式水力模型试验台,具备了按照IEC国际规程及GBT国家标准进行冲击式转轮水力研究试验的能力。同时,东方电气对高水头大容量冲击式水电机组转轮等核心部件的制造工艺进行专题技术攻关,具备了高水头大容量冲击式水电机组转轮研制能力。
2021年5月,东方电气签订“四川省田湾河流域梯级电站水斗式转轮国产化研究合作协议”,推进150兆瓦级大型冲击式转轮国产化相关工作。2021年12月,150兆瓦级大型冲击式转轮完成验证试验。2022年11月,150兆瓦级大型冲击式转轮水力模型通过验收。2023年5月,150兆瓦级大型冲击式转轮成功下线,开启了我国水力发电产业高质量发展的崭新篇章。
东方电气将以此为契机,进一步加强联合创新,携手国内能源企业,共同推进具有世界影响力的500兆瓦冲击式水电机组工程示范应用,接续开展更高水头大容量冲击式水电机组研制,持续推动我国水力发电产业高质量发展,为加快建设科技强国,更好服务“双碳”目标作出新的更大贡献。